The screw compressor was invented by Alf Lysholm, a professor at the Royal Swedish Institute of Technology, in 1934. Its original intention was to supercharge diesel engines and gas turbines. According to relevant statistics: during 3000 hours of operation, the failure of the piston unit is 10 times that of the screw unit; during 12,000 hours of operation, the failure of the piston unit is 4 times that of the screw unit. The screw machine is a rotary type, and its amplitude is 1/5 of that of the piston machine, so the vibration and noise are relatively small. At present, oil-injected screw compressors have become the main models in the fields of aerodynamics and refrigeration, and air conditioning. In the medium volume flow aerodynamic device and the medium cooling capacity refrigeration device, it occupies the dominant market share. In food, medicine and other industries, oil-free screw compressors are highly regarded as novel, clean, and efficient process compressors.
The core part of the screw compressor is the screw rotor. The advanced nature of the rotor profile determines the performance of the whole machine, and the requirements for processing accuracy and surface heat treatment are very high. Whether the most advanced molding line can be processed has become a symbol of measuring the economic strength and technical strength of a machining enterprise. At present, the rotor profile has been developed to the third generation - asymmetric profile, mainly including the German GHH profile, Japan's Hitachi profile, and Sweden's Atlas Copco SAP profile, using 5 to 6 asymmetric tooth profiles. Screw processing equipment and measuring and testing equipment are basically imported from abroad, mainly including the British HOLROYD machining center, German MAUSER, Italian DEA, British IMS three-coordinate measuring system, but the prices are very expensive, often tens of millions of yuan, and ordinary enterprises cannot afford it purchase and routine maintenance, so some domestic refrigeration unit manufacturers have two choices when producing or supplying: one is "bringing", that is, compressors or machine head parts are directly purchased from foreign professional manufacturers. At present, the international relatively high-quality compressor brands include Taiwan's HANBELL, Fusheng, Germany's BITZER, Grasso, Italy's REFCOMP, Fujihao, COMA, Japan's Hitachi, Daikin, Mitsubishi Heavy Industries, Kobelco, FRICK of the United States, Atlas Copco of Sweden; Evaporators, condensers, degreasers, etc. are processed domestically, plus some imported electrical controls Components (such as industrial programmable controllers PLC, programmable terminal touch screens, filters, thermal expansion valves, etc.) are assembled and shipped. . The second is "self-reliance", that is, except for electrical control components, machine head components, evaporators, and condensers are all processed and produced by themselves. The scale of the enterprise is generally relatively large, and all casting, processing and testing equipment are imported.
In order to ensure the normal, safe and reliable operation of the compressor, it is necessary to ensure that other components in the unit, including the condenser, evaporator, throttling or expansion valve, work normally, and a series of control components are also required to control the temperature and pressure parameters during the operation of the compressor. Real-time detection and feedback, and the normal operation of the whole machine is coordinated by the industrial programmable controller. These automatic protection functions must include high and low voltage protection, oil level protection, exhaust overheating protection, motor overheating and overcurrent protection, phase loss, and reverse-phase protection. , water cutoff protection, antifreeze protection, etc., in order to automatically stop the system, lock the fault, display alarm/warning information, and issue an alarm signal in the event of an abnormality in the system.
Refrigeration units are generally high-power power-consuming equipment, and their energy-saving requirements during operation are very important. It is required that the unit can automatically adjust the operating state according to external load changes to ensure that the unit operates under the optimal load. At the same time, the unit must have partial load performance, that is, it can operate effectively at a lower load and when the cooling tower water temperature is low, and realize step-less regulation. Naturally, the wider the energy regulation range, the better. In the design of refrigeration systems, economical economizers are often used to make part of the refrigerant liquid pass through the intermediate cooling to improve the degree of subcooling, thereby improving the refrigeration capacity per unit of working medium. In terms of measuring the power economy of the unit, the cooling capacity per unit of input power is an important parameter, and the sophisticated equipment can reach more than 4.5W/W, also known as the energy efficiency ratio or performance coefficient, which is expressed by COP (Coefficient of performance).
A friendly human-machine interface is also an essential part of a well-made refrigeration unit. It is generally required to use an industrial-grade programmable controller + touch screen operation with a full Chinese interface. This combination mode is simple and easy to understand, with strong anti-interference ability and a high degree of automation. Operators can freely change parameter settings according to actual production needs and have multiple functions such as "running status display", "failure cause display", "cumulative running time display", etc. The provided data information is complete and detailed, which is convenient for historical queries and maintenance
.
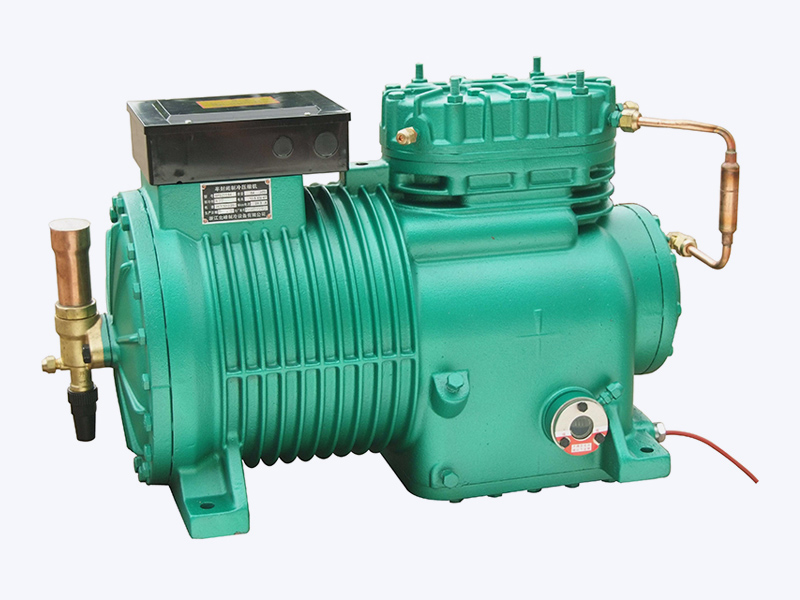