Regularly check these 9 parts of the industrial chiller, you can spend less money, and your peers will not tell you! In your factory or laboratory, the chillers are responsible for cooling and controlling the temperature of the production equipment. They are like a caring "care worker", cooling and controlling the temperature of the production equipment. Then you should treat them like your family, so as to prolong their life and promote production with quality and quantity.
Regular inspection of the following 9 parts can make the chiller more efficient, healthier and less expensive!
1. Maintenance of the compressor
Taking the screw compressor as an example, the screw is a precision component that determines the performance of the chiller. If you often work in bad conditions, there may be failures, and the maintenance cost is also very expensive. A small part may cost at least a thousand yuan, not to mention the labor cost. And if you can avoid failures through regular maintenance, you can save money. Generally, the inspection is carried out by professional qualified engineers, with a cycle of two years.
2. Regularly check the safety valve
The condenser is a major part of the chiller. On the screw chiller, the safety valve is installed on it. In order to avoid the impact of the high pressure of the condenser on the unit, the safety valve can play the purpose of automatic pressure relief. Therefore, it should be checked regularly to see if it is faulty and aging. If it fails, it must be replaced.
3. Regularly clean the scaled parts
For example, cooling water tower: larger chillers usually cool the condenser temperature through the cooling water tower, and the water tower circulates for a long time, it will also cause impurity pollution, scaling in the condenser tube, etc., causing damage to the unit. Therefore, cleaning the condenser regularly will help to keep the interior clean.
For example, condensers, evaporators, heat dissipation pipes, especially the connected parts, the chiller runs for a long time, and it is easy to produce scale, which in turn affects the cooling efficiency and heat dissipation of the unit. Therefore, the pipes should be cleaned according to the specific operating environment. Usually cleaned once every six months.
4. Regularly replace the lubricating oil
The chiller is also a mechanical equipment, and the operation also uses lubricating oil. After a long working time, the natural oil quality will deteriorate, and impurities such as air and moisture will penetrate into it. Therefore, it is a good thing to replace the chiller regularly. . Replace at least once a year.
5. Regular filter replacement
The filter drier is a component in the refrigeration system that filters moisture, so that the unit is filled with dry refrigerant to avoid moisture and damage to the refrigeration system. Therefore, the filter drier works all the time during the operation of the unit, and should be checked at least once a year, and should be checked once every six months in a harsh operating environment.
6. Check the amount of refrigerant in the chiller
If it is not enough, it is necessary to replenish the refrigerant in time to avoid insufficient cooling effect caused by too low, and also cause "burn" to the unit.
The following are some inspections and maintenance of electrical components and adjustment components.
7. Check whether the main circuit of the electronic control system is insulated to the outside
If it is in a humid environment, it should be checked frequently to ensure that the line is normal and there is no leakage.
8. Check the high and low pressure switches of the unit
The high and low pressure switch of the unit is a device to ensure the safety of the compressor. If the pressure exceeds or falls below the rated pressure, the line will be automatically cut off, and the compressor will stop working. If this group of values is not within the normal range, it will affect the use of the compressor.
9. Check the thermostat of the unit to ensure that the thermostat displays normally
The thermostat is a device that the staff directly controls the temperature. Only when it is displayed normally can the chiller work normally. Therefore, it should be regularly checked whether it is displayed and whether it is abnormal.
After the inspection of the above 9 parts is completed, it is necessary to test the machine to run, and perform a general calibration to test whether the superheat is normal, whether there are abnormal noises, odors and other abnormal situations. Regular inspection is the maintenance of each chiller equipment, which can prolong the use of the equipment for 3-6 years.
To summarize with you, the 9 parts of the chiller that need to be checked regularly are compressors, fouling-prone pipelines, safety valves, dryers, lubricating oils, refrigerants, line insulation, pressure switches, and temperature switches. In fact, it is easy to understand that the 4 major refrigeration components plus oil, electricity, water (water removal in the dryer), refrigerant and 2 switches for controlling pressure and temperature.
Regularly check these 9 parts of the chiller, don't wait until the equipment fails before spending money on repairs! Waste of money.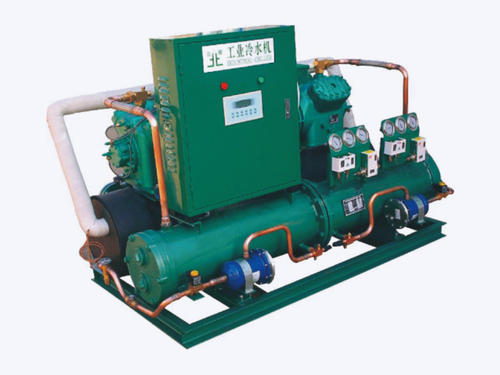
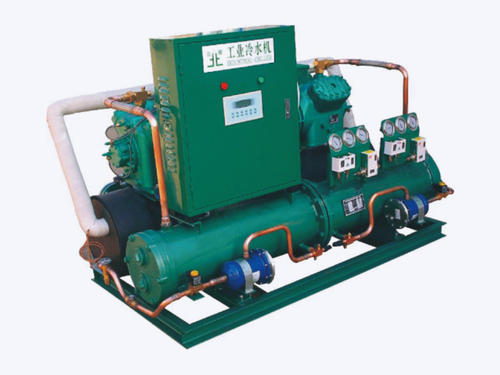