29
Mar
Chillers typically incorporate several safety features to prevent accidents or malfunctions. Some common safety features include:
High-pressure and Low-pressure Cutouts: High-pressure and low-pressure cutouts serve as vital safeguards within the chiller system, employing sophisticated pressure sensing devices strategically positioned throughout the refrigeration circuit. These sensors continuously monitor refrigerant pressure levels, transmitting real-time data to the chiller's control unit. In the event of pressure deviations beyond predetermined thresholds, indicative of potential system stress or malfunction, the chiller's control logic initiates an immediate shutdown sequence. This proactive response prevents the escalation of pressure-related issues, such as compressor overload, condenser coil failure, or refrigerant leaks, thereby preserving equipment integrity and ensuring operational safety.
Temperature Sensors: Temperature sensors form a crucial component of the chiller's sensory network, meticulously placed at critical junctures within the refrigeration cycle. These sensors constantly monitor the thermal dynamics of refrigerant streams, evaporator coils, condenser units, and other vital components. By continuously transmitting temperature data to the chiller's central control system, these sensors enable real-time monitoring and analysis of thermal behavior. Should temperatures deviate from optimal ranges, indicating potential system inefficiencies, component failures, or safety hazards such as refrigerant phase changes, the chiller promptly activates protective protocols, including shutdown sequences and alarm notifications. This preemptive approach mitigates the risk of thermal damage, equipment failure, and operational disruptions, ensuring the sustained reliability and safety of the chiller system.
Safety Relief Valves: Safety relief valves represent critical fail-safe mechanisms designed to protect the chiller system from overpressure conditions. Engineered to precise tolerances, these valves are strategically integrated into the refrigeration circuit, typically at high-pressure points prone to pressure buildup. In the event of pressure spikes exceeding safe operating limits, safety relief valves automatically engage, swiftly releasing excess pressure to prevent catastrophic system failures, such as ruptures or explosions. By alleviating pressure-induced stress, these valves ensure the continued operational safety and structural integrity of the chiller system, minimizing the risk of personnel injury, environmental contamination, and property damage.
Oil Pressure Monitoring: Oil pressure monitoring systems represent a critical safeguard within chiller units equipped with oil-lubricated compressors. These systems employ precision sensors to continuously assess oil pressure levels within compressor units, ensuring optimal lubrication and operational efficiency. Should oil pressure deviate from prescribed parameters, indicating potential lubrication system malfunctions, oil degradation, or compressor wear, the chiller initiates immediate corrective measures, including shutdown protocols and diagnostic notifications.
Leak Detection Sensors: Leak detection sensors play a pivotal role in identifying and mitigating refrigerant leaks within the chiller system. Employing advanced detection technologies, such as infrared spectroscopy or ionization-based sensors, these devices continuously monitor refrigerant levels and analyze ambient air quality for trace gas concentrations. Upon detecting anomalous readings indicative of refrigerant leakage, the chiller activates comprehensive response protocols, including immediate system shutdowns, alarm notifications, and leak isolation measures. This proactive approach minimizes environmental impact, protects personnel from exposure to hazardous substances, and preserves equipment integrity, ensuring the sustained operational safety and regulatory compliance of the chiller system.
Semi-Hermetic Industrial Chiller
High-pressure and Low-pressure Cutouts: High-pressure and low-pressure cutouts serve as vital safeguards within the chiller system, employing sophisticated pressure sensing devices strategically positioned throughout the refrigeration circuit. These sensors continuously monitor refrigerant pressure levels, transmitting real-time data to the chiller's control unit. In the event of pressure deviations beyond predetermined thresholds, indicative of potential system stress or malfunction, the chiller's control logic initiates an immediate shutdown sequence. This proactive response prevents the escalation of pressure-related issues, such as compressor overload, condenser coil failure, or refrigerant leaks, thereby preserving equipment integrity and ensuring operational safety.
Temperature Sensors: Temperature sensors form a crucial component of the chiller's sensory network, meticulously placed at critical junctures within the refrigeration cycle. These sensors constantly monitor the thermal dynamics of refrigerant streams, evaporator coils, condenser units, and other vital components. By continuously transmitting temperature data to the chiller's central control system, these sensors enable real-time monitoring and analysis of thermal behavior. Should temperatures deviate from optimal ranges, indicating potential system inefficiencies, component failures, or safety hazards such as refrigerant phase changes, the chiller promptly activates protective protocols, including shutdown sequences and alarm notifications. This preemptive approach mitigates the risk of thermal damage, equipment failure, and operational disruptions, ensuring the sustained reliability and safety of the chiller system.
Safety Relief Valves: Safety relief valves represent critical fail-safe mechanisms designed to protect the chiller system from overpressure conditions. Engineered to precise tolerances, these valves are strategically integrated into the refrigeration circuit, typically at high-pressure points prone to pressure buildup. In the event of pressure spikes exceeding safe operating limits, safety relief valves automatically engage, swiftly releasing excess pressure to prevent catastrophic system failures, such as ruptures or explosions. By alleviating pressure-induced stress, these valves ensure the continued operational safety and structural integrity of the chiller system, minimizing the risk of personnel injury, environmental contamination, and property damage.
Oil Pressure Monitoring: Oil pressure monitoring systems represent a critical safeguard within chiller units equipped with oil-lubricated compressors. These systems employ precision sensors to continuously assess oil pressure levels within compressor units, ensuring optimal lubrication and operational efficiency. Should oil pressure deviate from prescribed parameters, indicating potential lubrication system malfunctions, oil degradation, or compressor wear, the chiller initiates immediate corrective measures, including shutdown protocols and diagnostic notifications.
Leak Detection Sensors: Leak detection sensors play a pivotal role in identifying and mitigating refrigerant leaks within the chiller system. Employing advanced detection technologies, such as infrared spectroscopy or ionization-based sensors, these devices continuously monitor refrigerant levels and analyze ambient air quality for trace gas concentrations. Upon detecting anomalous readings indicative of refrigerant leakage, the chiller activates comprehensive response protocols, including immediate system shutdowns, alarm notifications, and leak isolation measures. This proactive approach minimizes environmental impact, protects personnel from exposure to hazardous substances, and preserves equipment integrity, ensuring the sustained operational safety and regulatory compliance of the chiller system.
Semi-Hermetic Industrial Chiller
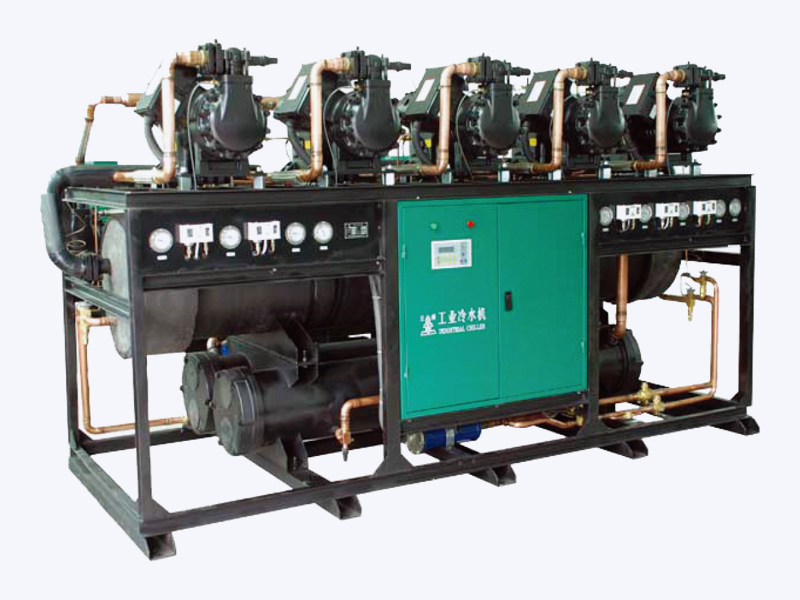