05
Mar
Preventing corrosion and scaling within a water-cooled condenser system is crucial for maintaining its efficiency and longevity. Several measures are commonly employed to address these issues:
Water Treatment: Water treatment is a multifaceted approach aimed at modifying the chemical composition of the water within the condenser system to mitigate scaling and corrosion. This involves the application of various chemical additives tailored to the specific water chemistry and operational conditions. Scale inhibitors function by interfering with the crystallization process of mineral compounds present in the water, thereby preventing the formation of scale deposits on heat exchange surfaces. Corrosion inhibitors create a protective layer on metal surfaces, inhibiting the electrochemical reactions responsible for corrosion. Dispersants aid in keeping suspended solids in the water dispersed, preventing their agglomeration and deposition as scale. The selection and dosing of these treatment chemicals are based on thorough water analysis and ongoing monitoring to ensure optimal performance and cost-effectiveness.
Water Filtration: Water filtration plays a critical role in maintaining water quality by removing particulate matter, sediment, and other impurities that can contribute to fouling and scaling within the condenser system. Filtration systems are designed to capture and retain suspended solids through various filtration media, including sand, activated carbon, and multimedia filters. The choice of filtration method depends on factors such as the size and type of contaminants present in the water, flow rates, and system requirements. Regular monitoring and maintenance of filtration equipment are necessary to ensure proper operation and prevent clogging or breakthrough of contaminants, which could compromise system performance.
pH Control: pH control is fundamental to corrosion management and scale prevention within the condenser system. The pH level of the circulating water influences the solubility of minerals and the corrosion susceptibility of metal surfaces. Maintaining the water within the recommended pH range—typically slightly alkaline to neutral—is crucial for minimizing corrosion rates and inhibiting scale formation. Chemical additives such as acids or alkalis are used to adjust and stabilize the pH of the water as needed. Continuous pH monitoring and control systems are often integrated into the condenser system to maintain optimal conditions and prevent fluctuations that could lead to corrosion or scaling issues.
Inhibitors: Corrosion inhibitors are chemical compounds specifically formulated to protect metal surfaces from corrosion by forming a passive protective layer that acts as a barrier against corrosive agents present in the water. Anodic inhibitors work by blocking the oxidation reactions that occur at the metal surface, while cathodic inhibitors inhibit the reduction reactions involved in corrosion processes. Mixed inhibitors combine both mechanisms to provide comprehensive corrosion protection. These inhibitors are typically added to the circulating water at controlled concentrations through automated dosing systems.
Regular Cleaning and Maintenance: Regular cleaning and maintenance procedures are essential for optimizing the performance and longevity of the condenser system by removing accumulated scale, sediment, and other deposits that can impede heat transfer and promote corrosion. Mechanical cleaning methods, such as brushing, rodding, or water jetting, are commonly used to dislodge and remove deposits from the internal surfaces of condenser tubes and heat exchanger coils. Chemical cleaning agents may also be applied to dissolve stubborn scale and corrosion deposits, followed by thorough rinsing to remove residues. Inspection and testing of system components for signs of wear, corrosion, or leakage should be performed routinely to identify potential issues early and prevent costly downtime or equipment failures.
Shell And Tube Water-Cooled Condenser
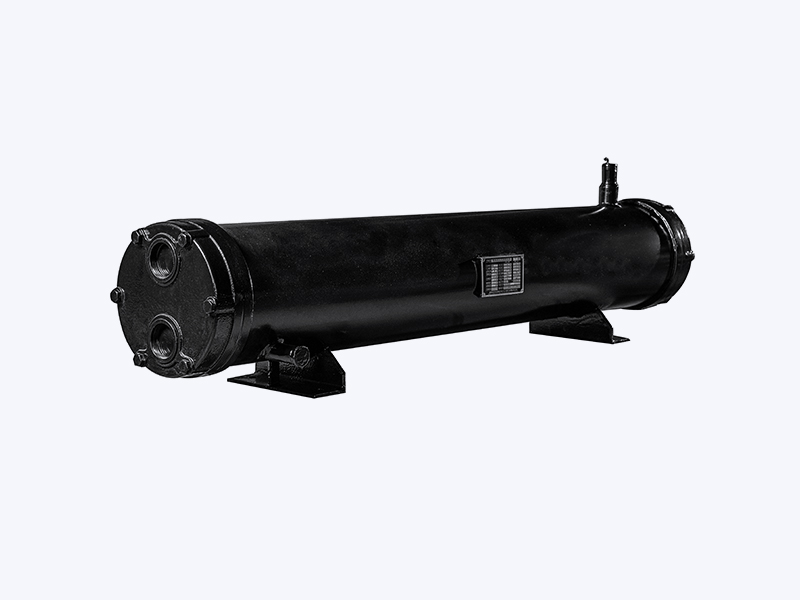
Shell And Tube Water-Cooled Condenser
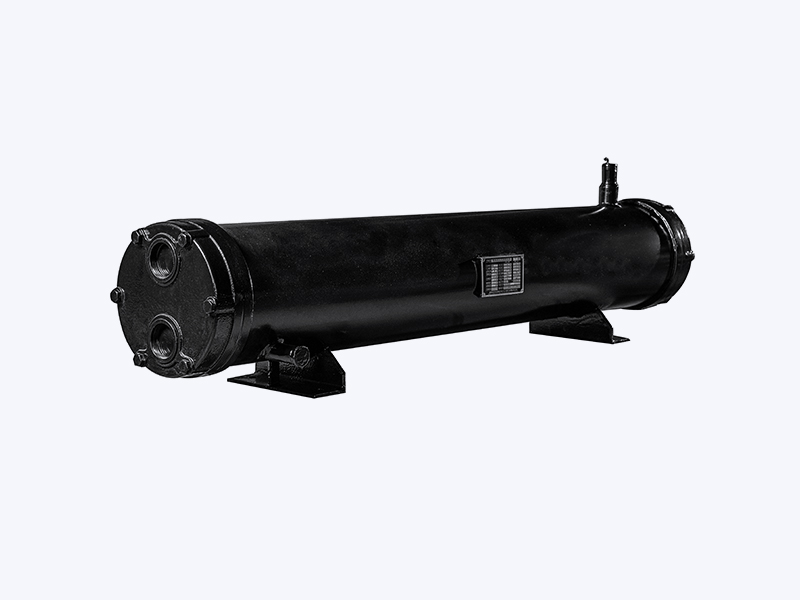