02
Oct
Safety is paramount when installing and maintaining air-cooled condensers. Here are key safety considerations:
1.Electrical Safety:
Disconnect and Lockout/Tagout Procedures: Before any electrical work on the air-cooled condenser, it is imperative to disconnect power sources and use lockout/tagout procedures to ensure that the unit remains de-energized during maintenance. Only qualified personnel should perform electrical work.
PPE: Use appropriate personal protective equipment, such as insulated gloves, safety goggles, and non-conductive tools, to prevent electrical hazards.
2.Ladder and Platform Safety:
Stable Access: Use stable and OSHA-compliant ladders or work platforms designed for the specific height requirements. Ensure they are positioned on level ground to prevent tipping.
Proper Use: Avoid overreaching while working from ladders or platforms to maintain balance and stability.
3.Fall Protection:
Fall Arrest Systems: When working on rooftops or elevated surfaces, adhere to fall protection regulations. Use safety harnesses, guardrails, and other fall arrest systems to prevent falls.
4.Hot Surfaces and Heat Exposure:
Cooling Period: Allow the air-cooled condenser to cool down after operation before performing maintenance to avoid burns or injuries.
Heat-Resistant Gear: Use heat-resistant clothing, gloves, and face shields when handling components that may become hot during operation.
5.Refrigerant Safety:
Refrigerant Identification: Identify the type of refrigerant used in the system and adhere to safety guidelines for that specific refrigerant, as different refrigerants have varying safety properties.
Leak Detection: Regularly check for refrigerant leaks using appropriate detection equipment, and address any leaks promptly.
6.Chemical Exposure:
Chemical Handling: When using chemicals for cleaning or maintenance, follow the manufacturer's recommendations for safe handling, storage, and disposal. Use appropriate PPE, such as gloves and masks, when working with chemicals.
7.Ventilation:
Adequate Airflow: Ensure that enclosed spaces where air-cooled condensers are located have adequate ventilation to prevent the accumulation of potentially harmful gases, such as refrigerant leaks.
8.Equipment Isolation:
Power Disconnection: Isolate the air-cooled condenser unit from the power source and shut off any relevant breakers or switches before beginning maintenance or repair work to prevent accidental energization.
9.Safety Signage:
Clear Signage: Use prominently displayed safety signage to alert personnel and passersby to ongoing maintenance work and potential hazards. Ensure the signage is clear and easy to understand.
10.Training and Certification:
Qualified Personnel: Ensure that individuals involved in installation and maintenance are properly trained, certified, and well-versed in safety procedures and protocols specific to air-cooled condenser systems.
11.Emergency Procedures:
Emergency Equipment: Have readily accessible first-aid kits, fire extinguishers, and emergency eyewash stations, as well as clear emergency exit routes. Personnel should be trained in emergency response procedures.
12.Lockout/Tagout:
Control Measures: Implement a comprehensive lockout/tagout system to secure the air-cooled condenser unit during maintenance, ensuring that only authorized personnel can restart the equipment after work is complete.
13.Environmental Impact:
Regulatory Compliance: Adhere to environmental regulations governing refrigerants and chemicals. Safely manage and document the handling and disposal of these substances to minimize environmental impact.
14.Documentation:
Record Keeping: Maintain accurate records of installation, maintenance, and safety procedures. This documentation serves as a reference for future work and aids in compliance with safety standards.
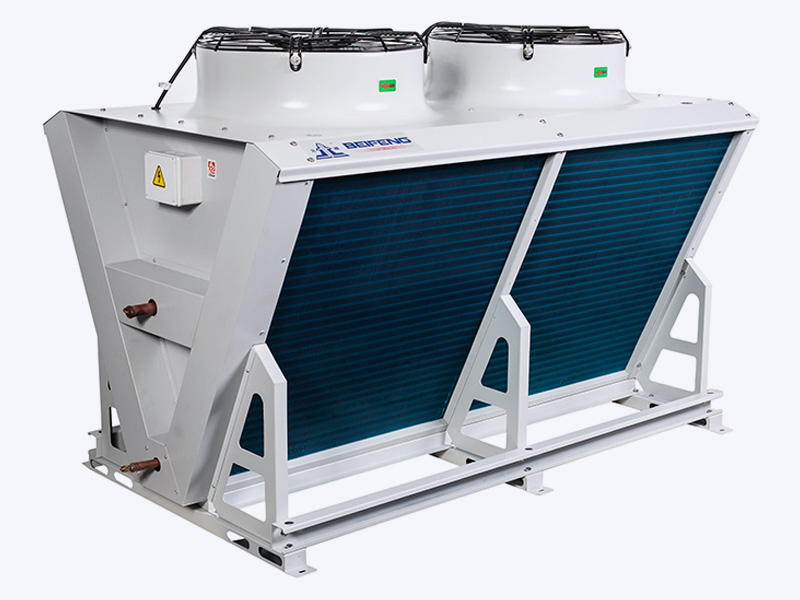
Adopt high technology in thermdynamics,combined the water condenser,cooling tower,recycle pump,as well as the connection tube.lt is well designed,energy and water safty, large heat exhange,smart structure.small sized.