In the realm of industrial and commercial facilities, the efficiency and reliability of chiller systems stand as cornerstones for maintaining optimal working environments. Chillers play a pivotal role in temperature regulation, serving diverse applications from HVAC systems to industrial processes. However, their seamless operation hinges on proactive management, rigorous maintenance, and strategic planning.
Common Causes of Chiller Failures:
1.Refrigerant Leaks:
Cause: Corrosion, vibration, or poor installation can lead to refrigerant leaks.
Prevention: Regularly inspect and maintain refrigerant lines, connections, and components.
2.Scale and Fouling:
Cause: Accumulation of scale, dirt, or other contaminants on heat exchanger surfaces.
Prevention: Implement a routine maintenance schedule for cleaning and water treatment.
3.Compressor Issues:
Cause: Overloading, electrical problems, or mechanical failures in the compressor.
Prevention: Regularly monitor operating conditions, conduct preventive maintenance, and ensure proper lubrication.
4.Electrical Failures:
Cause: Faulty electrical components, connections, or power supply issues.
Prevention: Regularly inspect and test electrical components, connections, and control systems.
5.Insufficient Refrigerant Charge:
Cause: Incorrect charging during installation or refrigerant leaks.
Prevention: Perform accurate refrigerant charging during installation and conduct regular leak checks.
Preventive Measures to Minimize Downtime:
1.Routine Maintenance: Establish a detailed maintenance schedule that includes daily, weekly, monthly, and annual tasks. Regularly inspect and clean condenser and evaporator coils, check refrigerant levels, and calibrate sensors. Replace worn-out components, such as belts and filters, as part of routine maintenance. Consider implementing a computerized maintenance management system (CMMS) for streamlined scheduling and tracking.
2.Water Treatment: Develop a comprehensive water treatment plan that addresses specific water quality issues for your geographic location. Conduct routine water testing to assess pH levels, hardness, and microbial content. Implement a combination of chemical treatments, such as corrosion inhibitors and biocides, tailored to the chiller system's requirements. Collaborate with water treatment specialists to customize a program that aligns with your facility's unique needs.
3.Monitoring and Analytics: Install a state-of-the-art monitoring system equipped with sensors, data loggers, and real-time analytics tools. Utilize machine learning algorithms to analyze historical data and predict potential failures. Implement remote monitoring capabilities to allow off-site analysis and immediate response to alarms. Integrate the monitoring system with a centralized control center for comprehensive oversight and quick decision-making.
4.Refrigerant Leak Detection: Deploy advanced refrigerant leak detection technologies, such as infrared sensors or ultrasonic detectors, to pinpoint leaks accurately. Implement a regular leak testing schedule, including electronic leak detection methods. Establish a protocol for rapid response, involving trained personnel equipped with appropriate safety gear and tools. Regularly update leak detection equipment to leverage the latest technological advancements.
5.Training and Documentation: Institute a comprehensive training program covering not only routine maintenance procedures but also emergency response protocols. Create detailed documentation, including troubleshooting guides, equipment history logs, and maintenance manuals. Develop an online knowledge repository accessible to maintenance staff for continuous learning. Conduct regular training sessions and knowledge-sharing forums to enhance the skills of maintenance personnel.
6.Load Optimization: Implement a dynamic load optimization strategy that leverages the latest control technologies. Utilize variable-speed drives to modulate chiller output based on real-time demand. Integrate intelligent control algorithms that adjust setpoints and operating parameters dynamically. Conduct regular energy audits to fine-tune load optimization strategies for peak efficiency. Collaborate with control system manufacturers to implement the latest load management features.
Semi-Hermetic Industrial Chiller
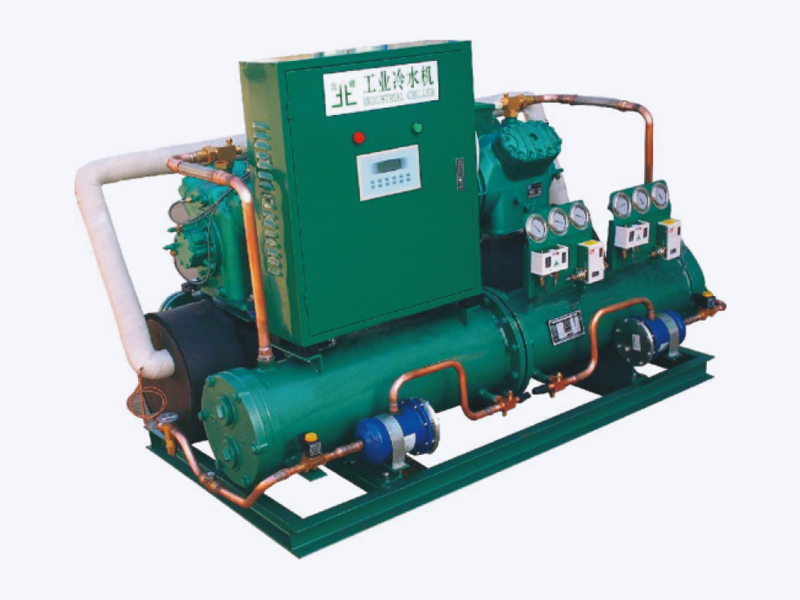
Semi-Hermetic Industrial Chiller
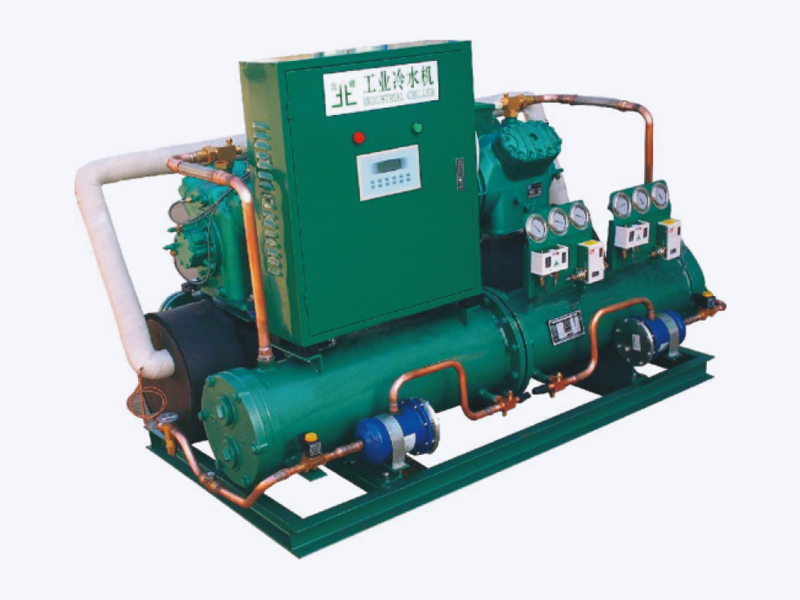