05
Apr
Optimizing the energy efficiency of an air-cooled condenser system is crucial for reducing operating costs and environmental impact. Here are some strategies to achieve this:
Proper Sizing: Properly sizing an air-cooled condenser involves a meticulous analysis of the cooling load requirements specific to the application. This entails considering not only the peak demand but also variations in ambient conditions throughout the year. Utilize sophisticated modeling software or consult with experienced engineers to account for factors such as solar radiation, prevailing wind patterns, and anticipated changes in heat load due to operational fluctuations. By accurately sizing the condenser, you not only optimize energy efficiency but also minimize initial capital expenditure and ensure long-term reliability.
Optimized Fan Control: The implementation of variable frequency drives (VFDs) or multi-speed fan motors enables granular control over fan speed, facilitating dynamic adjustment based on real-time cooling demand. However, the optimization of fan control extends beyond mere speed modulation. Integrate sophisticated control algorithms that factor in ambient temperature, system pressures, and thermal load variations to dynamically adjust fan speed and optimize energy consumption. Consider the integration of predictive maintenance algorithms to anticipate potential fan failures and proactively address issues before they impact system performance.
Airflow Management: Effective airflow management is pivotal to maximizing heat transfer efficiency and minimizing energy consumption in an air-cooled condenser system. Adopt a proactive approach to maintenance, implementing routine inspections and cleaning protocols to remove debris, dirt, and other contaminants that can accumulate on condenser coils and obstruct airflow. Consider implementing advanced airflow control mechanisms, such as variable inlet louvers or aerodynamic diffusers, to further enhance airflow management and reduce energy consumption.
Utilize Economizer Modes: Economizer modes offer a sophisticated means of harnessing ambient conditions to supplement or entirely replace mechanical cooling when feasible. However, the effective utilization of economizer modes requires more than just the activation of a switch. Implement intelligent control strategies that consider factors such as ambient temperature, humidity levels, and air quality to determine the optimal operating mode in real-time. Integrate predictive analytics capabilities to anticipate changes in weather patterns and preemptively transition between mechanical and economizer modes to maximize energy savings without compromising comfort or process requirements.
Optimal Set Points: Achieving optimal set points entails a nuanced balance between energy efficiency and operational performance. Leverage advanced control algorithms that take into account factors such as thermal inertia, system dynamics, and transient effects to establish set points that minimize energy consumption while ensuring adequate cooling capacity and system stability. Consider the integration of machine learning algorithms to continuously adapt set points based on historical data, seasonal trends, and evolving operational requirements, thereby maximizing energy efficiency and responsiveness over time.
Heat Recovery: Heat recovery presents a compelling opportunity to extract additional value from the air-cooled condenser system by repurposing waste heat for various applications. However, the effective implementation of heat recovery requires a comprehensive assessment of potential heat sources, heat sinks, and thermodynamic constraints. Conduct a detailed energy audit to identify opportunities for heat recovery within the system, such as recovering heat from condenser exhaust air for preheating water or space heating. Explore synergies with other processes or systems within the facility to maximize the utilization of recovered heat and minimize overall energy consumption.
BF-FNQ Serial Air-Cooled Condenser
Proper Sizing: Properly sizing an air-cooled condenser involves a meticulous analysis of the cooling load requirements specific to the application. This entails considering not only the peak demand but also variations in ambient conditions throughout the year. Utilize sophisticated modeling software or consult with experienced engineers to account for factors such as solar radiation, prevailing wind patterns, and anticipated changes in heat load due to operational fluctuations. By accurately sizing the condenser, you not only optimize energy efficiency but also minimize initial capital expenditure and ensure long-term reliability.
Optimized Fan Control: The implementation of variable frequency drives (VFDs) or multi-speed fan motors enables granular control over fan speed, facilitating dynamic adjustment based on real-time cooling demand. However, the optimization of fan control extends beyond mere speed modulation. Integrate sophisticated control algorithms that factor in ambient temperature, system pressures, and thermal load variations to dynamically adjust fan speed and optimize energy consumption. Consider the integration of predictive maintenance algorithms to anticipate potential fan failures and proactively address issues before they impact system performance.
Airflow Management: Effective airflow management is pivotal to maximizing heat transfer efficiency and minimizing energy consumption in an air-cooled condenser system. Adopt a proactive approach to maintenance, implementing routine inspections and cleaning protocols to remove debris, dirt, and other contaminants that can accumulate on condenser coils and obstruct airflow. Consider implementing advanced airflow control mechanisms, such as variable inlet louvers or aerodynamic diffusers, to further enhance airflow management and reduce energy consumption.
Utilize Economizer Modes: Economizer modes offer a sophisticated means of harnessing ambient conditions to supplement or entirely replace mechanical cooling when feasible. However, the effective utilization of economizer modes requires more than just the activation of a switch. Implement intelligent control strategies that consider factors such as ambient temperature, humidity levels, and air quality to determine the optimal operating mode in real-time. Integrate predictive analytics capabilities to anticipate changes in weather patterns and preemptively transition between mechanical and economizer modes to maximize energy savings without compromising comfort or process requirements.
Optimal Set Points: Achieving optimal set points entails a nuanced balance between energy efficiency and operational performance. Leverage advanced control algorithms that take into account factors such as thermal inertia, system dynamics, and transient effects to establish set points that minimize energy consumption while ensuring adequate cooling capacity and system stability. Consider the integration of machine learning algorithms to continuously adapt set points based on historical data, seasonal trends, and evolving operational requirements, thereby maximizing energy efficiency and responsiveness over time.
Heat Recovery: Heat recovery presents a compelling opportunity to extract additional value from the air-cooled condenser system by repurposing waste heat for various applications. However, the effective implementation of heat recovery requires a comprehensive assessment of potential heat sources, heat sinks, and thermodynamic constraints. Conduct a detailed energy audit to identify opportunities for heat recovery within the system, such as recovering heat from condenser exhaust air for preheating water or space heating. Explore synergies with other processes or systems within the facility to maximize the utilization of recovered heat and minimize overall energy consumption.
BF-FNQ Serial Air-Cooled Condenser
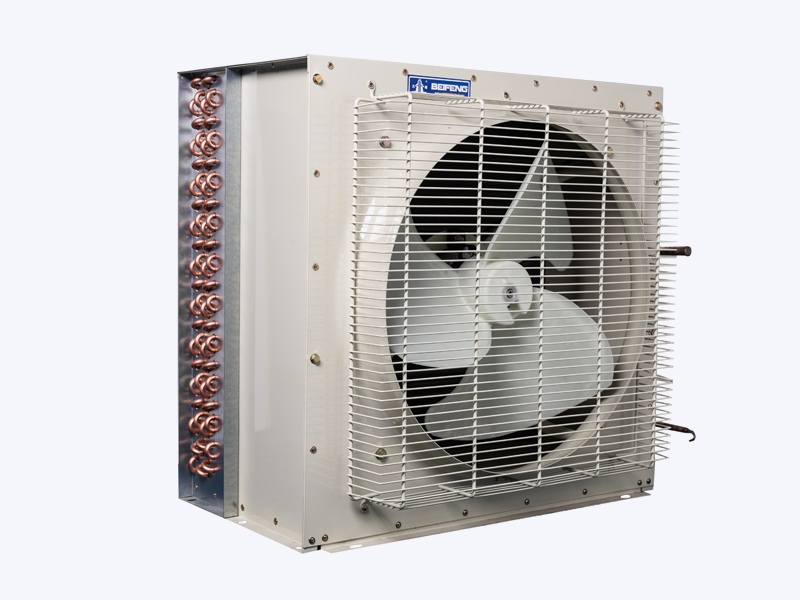