Troubleshooting and diagnosing common issues with semi-hermetic compressors in refrigeration systems is a crucial skill for maintaining system efficiency. Here are the steps to help you identify and address problems:
1.Check for Visible Damage:
Conduct a thorough visual inspection of the compressor, looking for signs of physical damage such as refrigerant leaks, oil stains, bent or damaged pipes, and loose or disconnected components. Document any visible issues for further assessment.
2.Listen for Unusual Sounds:
Start the compressor and carefully listen for any abnormal sounds. Knocks, rattles, screeches, or grinding noises may indicate mechanical problems, such as worn bearings or damaged internal components. Identifying these sounds early can prevent major failures.
3.Monitor Operating Parameters:
Use specialized gauges and sensors to measure and record critical operating parameters, including discharge and suction pressures, temperatures at various points in the system, and current draw. Compare these readings against manufacturer specifications to identify discrepancies.
4.Check Electrical Connections:
Inspect all electrical connections, terminals, and wiring associated with the compressor motor and control circuitry. Look for signs of corrosion, overheating, loose connections, or damaged insulation. Ensure the compressor is receiving the correct voltage and current to prevent electrical issues.
5.Refrigerant Leaks:
Utilize a refrigerant leak detector to systematically check the entire refrigeration system for leaks. If a leak is detected, locate and repair it promptly to prevent refrigerant loss, system inefficiency, and potential environmental concerns. After repairs, evacuate and recharge the system following proper procedures.
6.Oil Level and Quality:
Verify the compressor's oil level. Low oil levels can cause insufficient lubrication, leading to increased friction and wear within the compressor. Additionally, check the oil's quality for signs of contamination, ensuring it remains clean and free of debris.
7.Oil Pressure:
Measure and analyze oil pressure levels to confirm they fall within the specified range for the compressor model. Inadequate oil pressure can result in poor lubrication, potentially causing overheating and premature wear of internal components.
8.Suction and Discharge Pressures:
Compare measured suction and discharge pressures against recommended values provided by the manufacturer. Deviations may indicate issues such as refrigerant undercharge, overcharge, or problems with valves and pistons within the compressor.
9.Temperature Differentials:
Measure the temperature differentials across the evaporator and condenser coils. Proper heat transfer is essential for efficient operation. Deviations from expected differentials may point to issues with airflow, refrigerant flow, or fouling of coils.
10.Superheat and Subcooling:
Calculate and analyze superheat and subcooling values. Superheat measures the temperature increase of the refrigerant vapor above its boiling point, indicating proper evaporator operation. Subcooling measures the temperature decrease of the refrigerant liquid below its condensation point, ensuring efficient condensation. Deviations from recommended values may suggest problems in the system's thermal performance.
11.Motor Current Draw:
Use an ammeter to measure the compressor motor's current draw. Abnormally high or low current levels may indicate motor inefficiency, electrical issues, or mechanical problems within the compressor.
12.Vibration Analysis:
Employ vibration analysis tools and techniques to assess the compressor's vibration patterns. Excessive vibrations may signify misalignment, imbalanced components, or wear within the compressor. Addressing vibration issues promptly can prevent further damage and improve the compressor's lifespan.
Semi-Hermetic Two-Stage Compressor
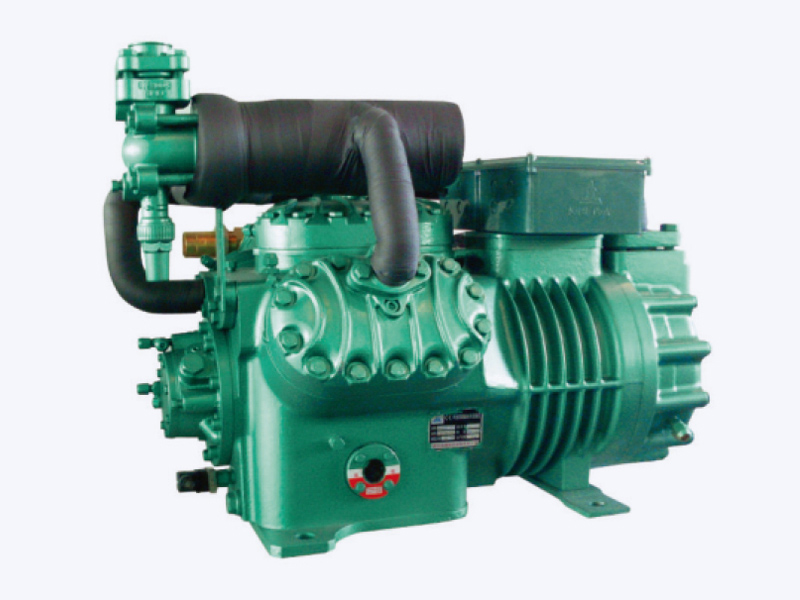
Semi-Hermetic Two-Stage Compressor
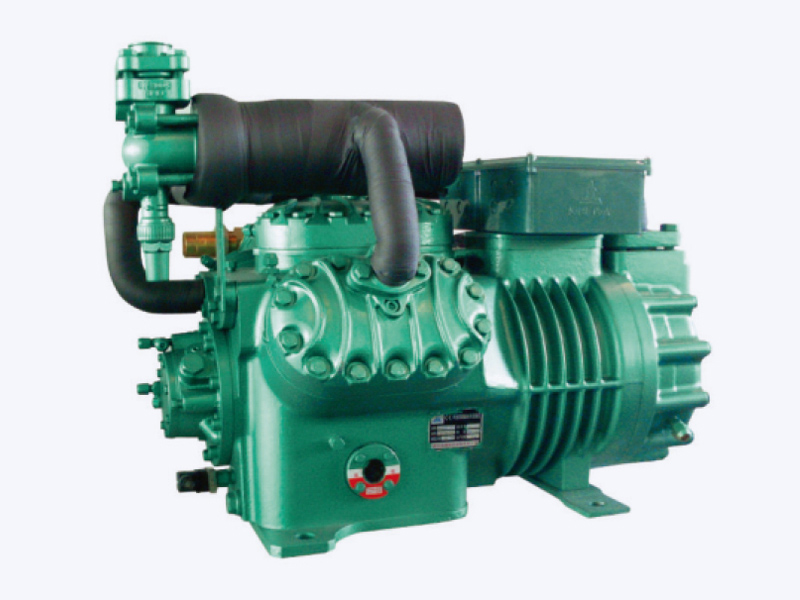