The efficiency of an air-cooled condenser can vary with changes in load or demand on the system due to several factors:
Heat Transfer Rate: The heat transfer rate within the condenser is a critical factor influencing its efficiency. When the system experiences changes in load or demand, such as increased production or environmental temperature variations, the heat load on the condenser changes accordingly. During periods of high demand, the condenser must effectively dissipate a greater amount of heat from the refrigerant to maintain optimal operating conditions. This requires the condenser to operate at higher capacities, increasing the heat transfer rate. Conversely, during lower demand periods, the heat transfer rate decreases as the condenser operates at reduced capacity. Maintaining an optimal heat transfer rate is essential for ensuring efficient cooling performance and preventing system overheating or inefficiencies.
Airflow: Changes in system load directly impact the airflow dynamics around the condenser coils. Higher loads require increased airflow to enhance heat exchange efficiency and prevent the condenser from becoming overwhelmed by heat accumulation. Adequate airflow is crucial for facilitating the transfer of heat from the refrigerant to the ambient air, ensuring efficient cooling. During peak load conditions, adjustments may be necessary to optimize airflow distribution and velocity across the condenser coils. This can be achieved through the use of adjustable louvers, variable-speed fans, or sophisticated control algorithms that modulate fan operation based on real-time load and ambient conditions. By optimizing airflow, the condenser can maintain consistent performance levels and minimize energy consumption under varying load conditions.
Fan Speed: Air-cooled condensers typically utilize fans to facilitate the movement of air across the condenser coils. Fan speed directly influences the airflow rate and, consequently, the condenser's cooling capacity. During periods of high demand, such as peak production hours or elevated ambient temperatures, the condenser may require increased fan speeds to enhance heat dissipation and maintain optimal operating temperatures. Higher fan speeds promote greater airflow over the coils, improving heat transfer efficiency and ensuring effective cooling performance. However, operating fans at higher speeds can result in increased energy consumption and noise levels, necessitating careful consideration of efficiency trade-offs. Modern condenser designs often incorporate variable-speed fan motors or intelligent control systems that dynamically adjust fan speed based on load conditions, optimizing energy efficiency while meeting cooling requirements.
Temperature Difference: The efficiency of the air-cooled condenser is influenced by the temperature differential between the refrigerant and the ambient air. During periods of varying load or demand, changes in operating conditions can affect the condensing temperature and, consequently, the temperature gradient across the condenser coils. Higher system loads typically result in elevated condensing temperatures, reducing the temperature difference between the refrigerant and the surrounding air. This narrowing of the temperature gradient can diminish the effectiveness of heat transfer and compromise condenser efficiency. To mitigate this effect, engineers may employ various strategies, such as increasing airflow rates, optimizing coil design and configuration, or adjusting refrigerant flow rates to maintain an adequate temperature differential.
Control Systems: Advanced control systems play a crucial role in optimizing the performance of air-cooled condensers in response to changing load conditions. These systems utilize sensors, actuators, and sophisticated algorithms to monitor key operating parameters, such as refrigerant temperature, ambient conditions, and system demand. By continuously analyzing real-time data, the control system can dynamically adjust various parameters, such as fan speed, refrigerant flow rates, and defrost cycles, to optimize condenser performance while minimizing energy consumption. Intelligent control strategies enable the condenser to adapt to fluctuating load conditions, ensuring efficient operation and reliable cooling performance.
FN Serial Air-Cooled Condenser
Heat Transfer Rate: The heat transfer rate within the condenser is a critical factor influencing its efficiency. When the system experiences changes in load or demand, such as increased production or environmental temperature variations, the heat load on the condenser changes accordingly. During periods of high demand, the condenser must effectively dissipate a greater amount of heat from the refrigerant to maintain optimal operating conditions. This requires the condenser to operate at higher capacities, increasing the heat transfer rate. Conversely, during lower demand periods, the heat transfer rate decreases as the condenser operates at reduced capacity. Maintaining an optimal heat transfer rate is essential for ensuring efficient cooling performance and preventing system overheating or inefficiencies.
Airflow: Changes in system load directly impact the airflow dynamics around the condenser coils. Higher loads require increased airflow to enhance heat exchange efficiency and prevent the condenser from becoming overwhelmed by heat accumulation. Adequate airflow is crucial for facilitating the transfer of heat from the refrigerant to the ambient air, ensuring efficient cooling. During peak load conditions, adjustments may be necessary to optimize airflow distribution and velocity across the condenser coils. This can be achieved through the use of adjustable louvers, variable-speed fans, or sophisticated control algorithms that modulate fan operation based on real-time load and ambient conditions. By optimizing airflow, the condenser can maintain consistent performance levels and minimize energy consumption under varying load conditions.
Fan Speed: Air-cooled condensers typically utilize fans to facilitate the movement of air across the condenser coils. Fan speed directly influences the airflow rate and, consequently, the condenser's cooling capacity. During periods of high demand, such as peak production hours or elevated ambient temperatures, the condenser may require increased fan speeds to enhance heat dissipation and maintain optimal operating temperatures. Higher fan speeds promote greater airflow over the coils, improving heat transfer efficiency and ensuring effective cooling performance. However, operating fans at higher speeds can result in increased energy consumption and noise levels, necessitating careful consideration of efficiency trade-offs. Modern condenser designs often incorporate variable-speed fan motors or intelligent control systems that dynamically adjust fan speed based on load conditions, optimizing energy efficiency while meeting cooling requirements.
Temperature Difference: The efficiency of the air-cooled condenser is influenced by the temperature differential between the refrigerant and the ambient air. During periods of varying load or demand, changes in operating conditions can affect the condensing temperature and, consequently, the temperature gradient across the condenser coils. Higher system loads typically result in elevated condensing temperatures, reducing the temperature difference between the refrigerant and the surrounding air. This narrowing of the temperature gradient can diminish the effectiveness of heat transfer and compromise condenser efficiency. To mitigate this effect, engineers may employ various strategies, such as increasing airflow rates, optimizing coil design and configuration, or adjusting refrigerant flow rates to maintain an adequate temperature differential.
Control Systems: Advanced control systems play a crucial role in optimizing the performance of air-cooled condensers in response to changing load conditions. These systems utilize sensors, actuators, and sophisticated algorithms to monitor key operating parameters, such as refrigerant temperature, ambient conditions, and system demand. By continuously analyzing real-time data, the control system can dynamically adjust various parameters, such as fan speed, refrigerant flow rates, and defrost cycles, to optimize condenser performance while minimizing energy consumption. Intelligent control strategies enable the condenser to adapt to fluctuating load conditions, ensuring efficient operation and reliable cooling performance.
FN Serial Air-Cooled Condenser
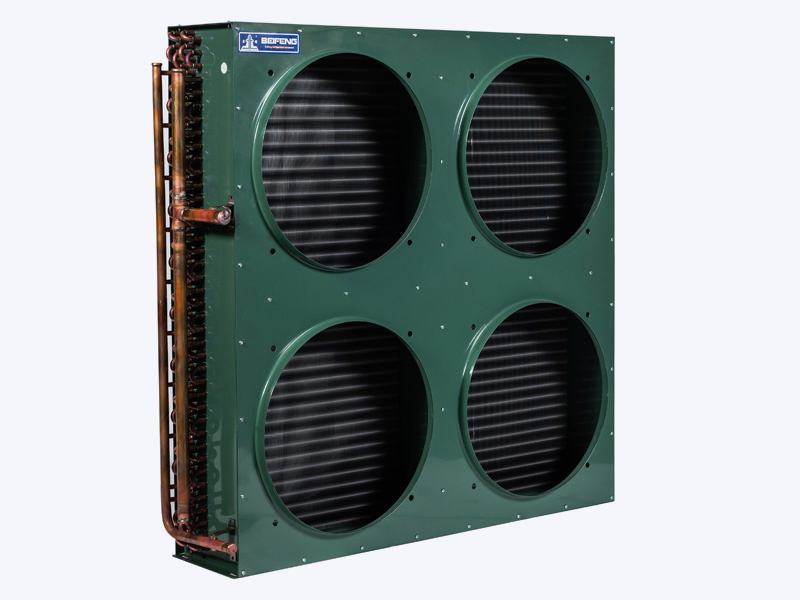